Global Franchise Supply Chain Management Is Critical for International Success
The Lexico Oxford Dictionary defines supply chain as “the sequence of processes involved in the production and distribution of a commodity.”
Effective and efficient global supply chain development and management are critical to a franchisor’s success and to maximizing unit royalties around the world.
As consumers, our usual supply chain concern is whether or not our favorite clothing store has our size in stock in a store or online. For franchisors who do business outside of their home country, supply chain development and management is a major ongoing challenge. In the best of times, franchisors in the food and beverage and retail sectors devote considerable time and money to ensure their products reach their international licensees in a timely and financially efficient manner.
Then, in the early months of 2020, Covid-19 happened. Stores and restaurants shut down worldwide. Orders for new products stopped. Shipping schedules went haywire and containers were left at ports where they were not needed. Air cargo shipments dramatically increased, along with the price of shipping. Local suppliers of food products shut down their production facilities. Consumers shopped online worldwide more than ever before.
In late 2020, when businesses began to start up again, stores and restaurants had to restock. Consumers started spending again at restaurants, creating high demand for food and associated products. But factories and food production facilities had to ramp back up. Shipping had to totally restart. What did this mean for franchisors and international franchisees?
I asked Tom Healey, Vice President of International Supply Chain and Product Development at Dairy Queen, for his take on the global supply chain in mid-2021. Dairy Queen has nearly 7,000 stores in almost 30 countries. Here’s his response:
At no time in recent history have supply chains in all sectors been this challenged across the globe as they face unprecedented circumstances having to manage multiple “everyday” supply chain needs all at once: labor, inflation, logistics, ongoing pandemic surges, economies closing and reopening, currency valuation and fluctuations, and global supply availability.
Production facilities around the globe are challenged not only with Covid-19 breakouts, but also by labor issues and/or government-funded unemployment benefits negatively affecting factory workforce availability and causing unforeseen inventory shortages. This has caused standard lead times to double or triple for normal planning practices. Ground, sea, and air freight pricing has increased more than 100%. Coupled with limited availability of transport vehicles, this has further exacerbated supply chain shortages.
To help mitigate the ongoing supply chain challenges a company should consider employing the following business practices:
- Have effective business continuity plans that identify critical business processes and the necessary recovery steps to limit financial or operational impact, while improving organizational resilience during and after an event.
- Diversifying your sourcing can have real financial impact on a company. The best prices are usually dependent on volume purchasing, so diluting your sourcing to several suppliers can increase your costs. Multiple suppliers may still be vulnerable if they are all in the same country or region. Each of your suppliers has traditional supply chains of their own.
- Since much of the extended supply chain is outside of your direct control, you must expand your sphere of influence in other ways. Make sure that you understand your suppliers’ security practices, quality controls, business maturity, and the overall value of working with a reliable partner versus focusing on lowest cost.
- A global supply chain is entirely dependent on transportation networks, so it may seem there is little a company can do to manage this risk. The global supply chain increases risk because of: 1) longer lead times to move raw materials and products; 2) political, economic, or regulatory disruption or instability affecting international sources; 3) port congestion or delays because of foreign regulations and customs problems; and 4) the impact of unforeseen tariffs or other roadblocks.
- Work with your partners to evaluate and mitigate risks to the supply chain. This includes suppliers, transportation providers, and customers to make sure that disruptions to the extended supply chain are part of their business continuity plan.
William Edwards is CEO of Edwards Global Services (EGS) and a global advisor to CEOs. From initial global market research and country prioritization to developing new international markets and providing operational support around the world, EGS offers a complete international operations and development solution for franchisors based on experience, knowledge, a team on the ground in more than 40 countries, and trademarked processes based on decades of problem-solving. Contact him at [email protected] or +1-949-224-3896. Read his latest biweekly global business newsletter at www.geowizard.biz.
Share this Feature
Recommended Reading:
FRANCHISE TOPICS
- Multi-Unit Franchising
- Get Started in Franchising
- Franchise Growth
- Franchise Operations
- Open New Units
- Franchise Leadership
- Franchise Marketing
- Technology
- Franchise Law
- Franchise Awards
- Franchise Rankings
- Franchise Trends
- Franchise Development
- Featured Franchise Stories
FEATURED IN
Franchise Update Magazine: Issue 3, 2021
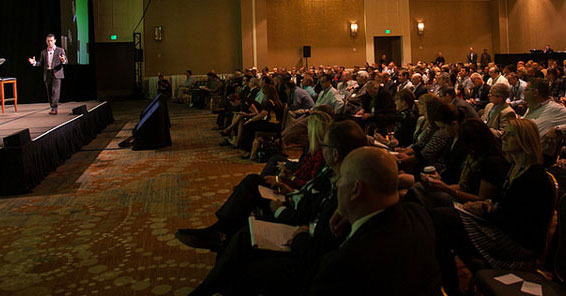